Diese Case Study ist auch auf Deutsch verfügbar
In addition to the process definition, development of a corresponding architecture, and the rollout, the focus was on user experience (UX) design, knowhow transfer, and onboarding of new employees. One of the greatest challenges was to combine the country-specific particulars in a single standard software: Now at all METRO sites, the warehoused products can be collected simply, efficiently, and quickly in accordance with customer specifications and be packed optimally for transport.
METRO is a leading international wholesaler with food and non-food product ranges; specializing in the needs of hotels, restaurants, and caters (HoReCa) as well as independent retailers. The company is active in 36 countries. The approximately 24 million METRO customers worldwide have the option of buying in one of the large markets, picking up online orders there, or getting their orders delivered. Through digitalization, the company positions itself as a future-oriented supplier in the sector. Interactions with the customer are handled via multiple sales channels (omni-channel), and interactive solutions ensure greater efficiency in day-to-day business. The newly developed offerings of METRO’s own IT subsidiary METRONOM contribute to further differentiation in the business and ensure better identification of the needs of customers.
Customized delivery to the customer
METRO works continuously to maintain and expand its competitive edge through new concepts, solutions, and mechanisms. The delivery service of METRO, which supplies primarily the hotel and hospitality sector, meets this challenge using business domains and verticals in a scalable structure along the complete customer journey.
This is supported by a completely new version of the entire shop, pick & pack, and warehouse management system M|SUITE. The verticalization in M|SUITE, which is broken down into the areas of M|SHOP and M|FULFILL, is now based on about 100 microservices. FULFILL is comprised of six verticals: Checkout, Order Management, Depot Management, Pick & Pack, Transport, and Driver App. In the overall project, INNOQ had independent responsibility for the product development of the verticalized system Pick & Pack.
The daily, time-critical delivery process is the unique selling proposition of the verticalized system Pick & Pack and also the challenge for the team.
Tobias EckardtBusiness Analyst at INNOQ
As a rule, the customers supplied in the food and hospitality sector order their desired goods as late as 3:00 p.m., and in some countries even into the evening. On average, METRO handles 125,000 orders a week. The processes at METRO run full speed to ensure delivery of the goods the next day as ordered: Some goods still have to be procured; fresh goods are not delivered to the depot until nighttime; the transport containers (trolleys or boxes) are picked and packed during the night and loaded on trucks. A depot contains 5,000 to 10,000 items, which are used exclusively for deliveries to the customers.
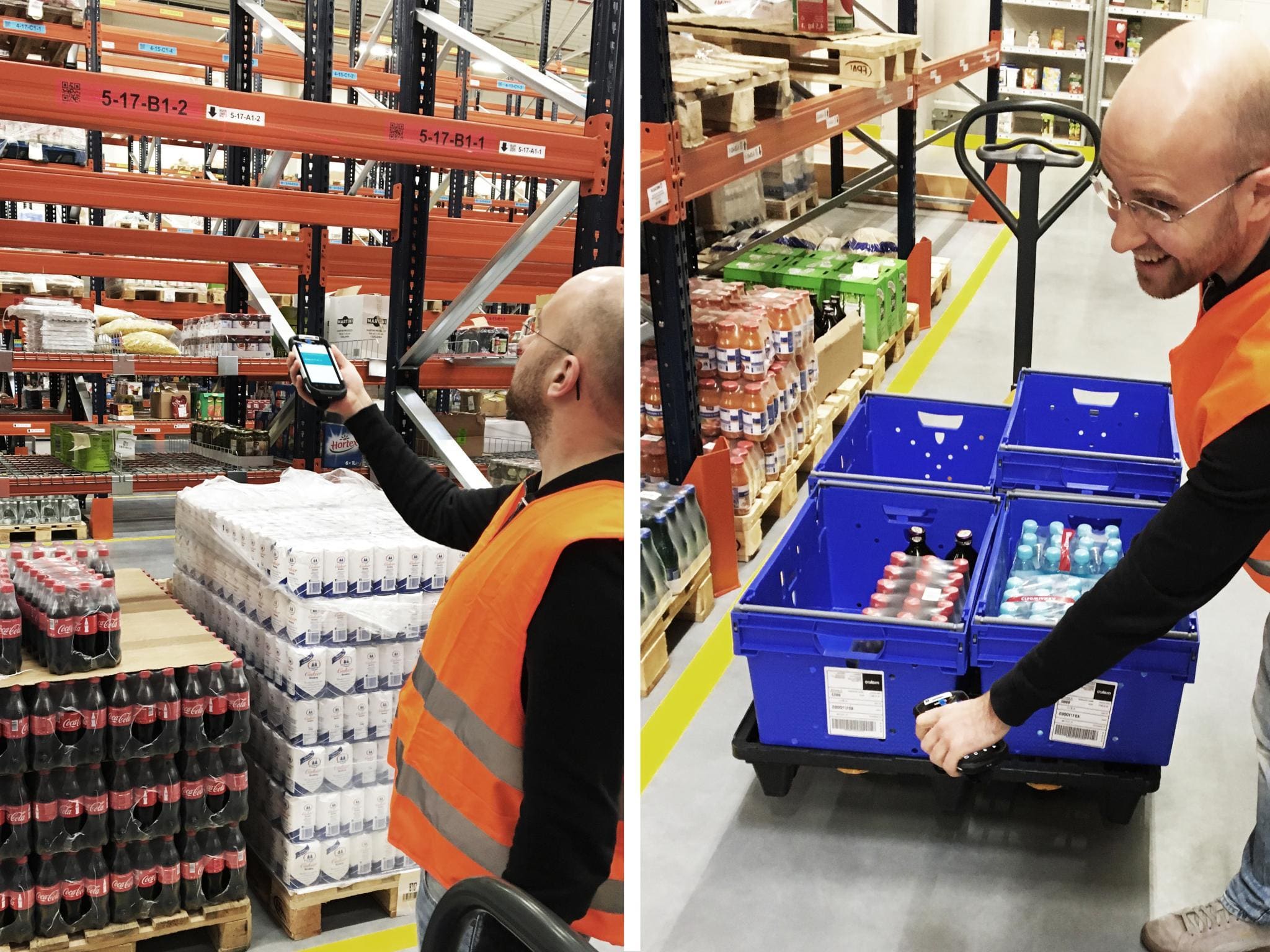
The goal of the IT project is to ensure that products in the pick & pack area can be assembled as ordered in such a way that the deliveries can be picked and packed for transport as simply, efficiently, and quickly as possible. The response time for missing items was to be minimized and the narrow time window for central picking utilized optimally during the night.
The initial requirements were defined by METRONOM, the central IT unit at METRO, with the international METRO sales lines. INNOQ worked up and prioritized the concrete feature requests with the countries on the management level and also incorporated feedback from the individual depots into the next iteration.
Olaf, in your view, what is the greatest benefit of Vertical Pick & Pack?
The standard software with adaptations to the various situations in the countries enables employees in the depot to pick and pack the goods for the end customers and make them available for loading on the truck simply and in a time-saving manner. The core of the software is logistically optimized truck dispatching, which results in better utilization and is thus more economical and ecological. In particular, from our depots in Poland, we got the positive feedback that the software enabled them to adjust perfectly to changes in orders during the course of the day and to utilize the trucks optimally.
What were the particular challenges in Vertical Pick & Pack?
The team in Vertical Pick & Pack, consisting of about 20 employees, was actually too large for agile work. We could have easily divided the verticals into three more verticals, but, because of the great interdependencies, we decided against it. Instead, we formed the teams Picking, Wave Planning, and Outbound Monitoring, which have coordinated closely with one another and, together, have prioritized the most important points.
Another big challenge was efficient team management for daily deployment. INNOQ made it possible through smoke tests and 24/7 second level support.
In your view, what was the particular added value of collaboration with INNOQ?
Above all, INNOQ supported us with its enormous technical knowhow. The consultants work agilely und understand a lot about change management in the context of digitalization. They are pros in verticalization and in software architecture. They analyzed the process quickly and competently, independently identified the concrete requirements, and evaluated possible solutions. They cooperated closely with me and the other verticals to drive implementation forward. If I may be permitted a comparison, it was like an ant hill, where each one knows its task precisely. Above all, I liked the structured way in which new employees were familiarized with the process and the tasks.
In the project period of more than three years, during which up to 20 employees from INNOQ participated, there were various phases of development. In each phase of development, the team based its work on the site-related requirements of METRO.
Through user tests close to the users
Regular user tests and interviews ensured that the software would be aligned closely to the needs of the users. Slicing the M|FULFILL process into verticals made it important to consider not only the development in the system Pick & Pack, but also interdependencies with other verticals.
Development and support
Parallel to the original Pick & Pack software, the three INNOQ teams Picking, Wave Planning, and Outbound Monitoring developed important add-ons. In particular, this included a new, easier-to-use user interface for mobile picking devices and desktop picking, support for multi-order picking (one picker collects items for multiple orders in one warehouse run), and support for stock normalization (management of the inventory in regard to smallest package size). In addition, in multi-order picking, route optimization was implemented for the aisles traveled in the depot.
Thanks to automatic deployment and almost completely automated test methods, the system is updated every day, in order to integrate updates into operations on a continuing basis. To ensure that the customers supplied by METRO receive their deliveries without interruption, the INNOQ team has taken over 24/7 second level support. Deeply integrated system monitoring, consisting of centralized logging, analytics, and proactive monitoring of applications, makes it possible to see at a glance where intervention is needed, so that everything runs smoothly at METRO.
The consultants work agilely and understand a lot about change management in the context of digitalization. They are pros in verticalization and in software architecture.
Olaf BergmannProduct Owner M FULFILL at METRO
Onboarding and knowledge transfer
Throughout the entire period of the project, INNOQ continuously integrated new developers. In the final phase, METRONOM-internal developers from Germany and Romania were gradually familiarized with the project, so that they could provide support in the future. To ensure that new personnel could be integrated efficiently and quickly, the INNOQ team independently created a structure for onboarding and knowledge transfer. In addition to continuous reviews and pair programming between experienced and less experienced developers, continuous documentation and updating of the software and application case studies facilitated knowledge transfer. For instance, the findings from our user experience research were transferred reliably to software development and then, to the satisfaction of users, were implemented in the standard software.
- Microservices architecture, adapted to the situation of the organization
- Uniform front end (UI) via M:FULFILL, but not across all verticals
- Mobile app (Android) or desktop (web-based)
- Role-based views: Supervisor UI and worker UI
- Multi-datacenter
- Deployment and operation with cloud services
- Monitoring with alerts